Personnel, digitalisation and rising costs – the major challenges of the logistics sector
Spain’s logistics sector is developing positively with annual growth rates of 3.20 % since 2017. The sector accounts for 6.9% of Spain’s GDP and benefits from the country’s well-developed infrastructure, increasing investments and geographical location. However, the industry is facing major challenges, above all a lack of skilled workers, digitalisation and rising costs.
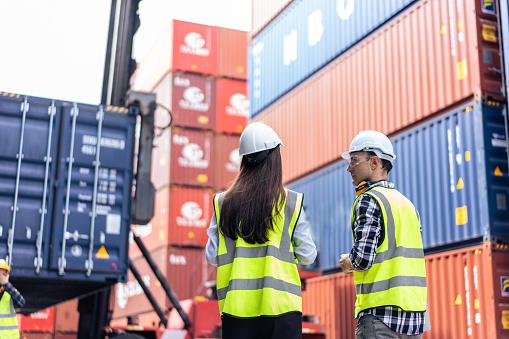
This is the conclusion of a recent market survey of entrepreneurs in the logistics and packaging sector conducted by Easyfairs, the organiser of Empack and Logistics & Automation. The uncertainties and challenges on the part of companies are contrasted by massive investments by the state in infrastructure. In particular, investments in new high-speed rail lines, freeing up conventional train lines for freight, and the strengthening of ports and airports are expected to strengthen intermodal connectivity and increase the speed of logistics movements throughout the country, as well as connections at an international level.
Road remains the main transport mode in Spain for the time being, with estimated annual growth rates of 5.16%. This further underlines the urgency of shifting freight traffic to other transport routes. For the necessary shift to rail alone, 24.2 billion € are to be invested by 2026. In the current Logistics Performance Index of the World Bank, Spain has thus moved up from 17th to 13th place.
Uncertainties and challenges for the future
The Spanish logistics and transport sector is highly fragmented. The five largest competitors have a combined market share of just about 6.4 %. The resulting high competition for market share and resources further exacerbates the challenges. Nevertheless, most respondents are positive about the overall outlook for their company or industry.
Skills shortage
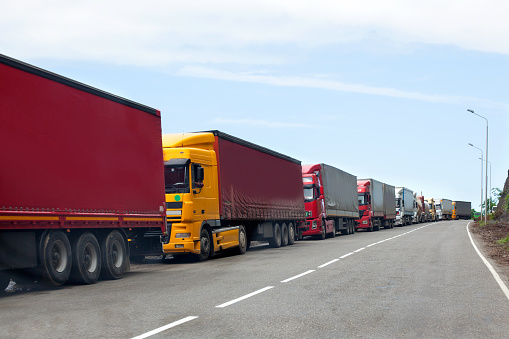
39.7 % of respondents in the logistics sector see the lack of qualified personnel as the biggest challenge. And the need is there. About one million new jobs have been created in recent years. In the CEP sector alone, the number of employees has grown by 2 to 4 % annually since 2019. However, these impressive numbers mask two fundamental problems that, taken together, will exacerbate the shortage of qualified personnel in the future. For some years now, not all vacancies can be filled and in some occupational fields, e.g. lorry drivers, there is a particular lack of young recruits. When the older workers retire, the problem will become even more acute.
Rising costs for fuel and personnel
The rising costs of fuel and personnel are causing problems for many companies in particular, with around a third of the companies surveyed in the transport sector citing this area as the biggest challenge. Prices for petrol have risen by 12 % since January 2023 alone. In contrast, despite partial price adjustments, revenues could not be increased accordingly to cover the costs.
Technological innovation
Innovation and investment in new technologies is seen as a continuing challenge by 31 % of the logistics companies surveyed. In the transport sector, it is even two-thirds. A particularly interesting finding of the Easyfair study is not so much that the transport and logistics sector is late in tackling technological modernisation. In fact, the results of the study show that the delayed introduction of new technologies is mainly due to resistance to change (33.2%) and high start-up costs (29.5%). 20 % even state that there is a lack of knowledge and skills in their company to introduce new technologies.
However, the vast majority believe that the widespread adoption of robotics and artificial intelligence will be undeniable, as will the significant change they will bring to the industry. The most commonly used robotic tools in the industry are mainly automated transport systems (28.4%), collaborative robots (26.3%), followed by robotic handling and packaging systems (26.3%).
Excursus: Investment in sustainability
Another factor is the increasing demand on the customer side for sustainable shipping solutions, also in Spain. Investment in sustainability is an important factor for almost all companies in the sector (95.3%), even if not all of them attach the same importance to this factor. Similarly, 33.7% believe that there are other areas of investment that have a higher priority, such as digitalisation, although they also see sustainability as important.
How companies can respond to the challenges
When asked about their strategy to combat rising expenses and financing costs, the vast majority of companies are focusing on increasing efficiency and optimising operations (76.8%) and reducing costs (25.8%), according to the Easyfair survey. At the same time, however, companies increasingly have to compete not only for market share but also for staff. The associated rising costs will inevitably be passed on to customers, even if only proportionately. This is because measures to increase efficiency and investments in new technologies will be associated with high initial costs, whereas the cost reduction effects will only occur in the medium term. In addition, there are risks for the own supply chain if the own goods are no longer reliably delivered due to staff or capacity bottlenecks at the logistics providers.
Multi-carrier service providers such as LetMeShip support small and medium-sized B2B companies in optimising their own shipping processes and reducing costs as well as creating full transparency over all costs and goods transports.